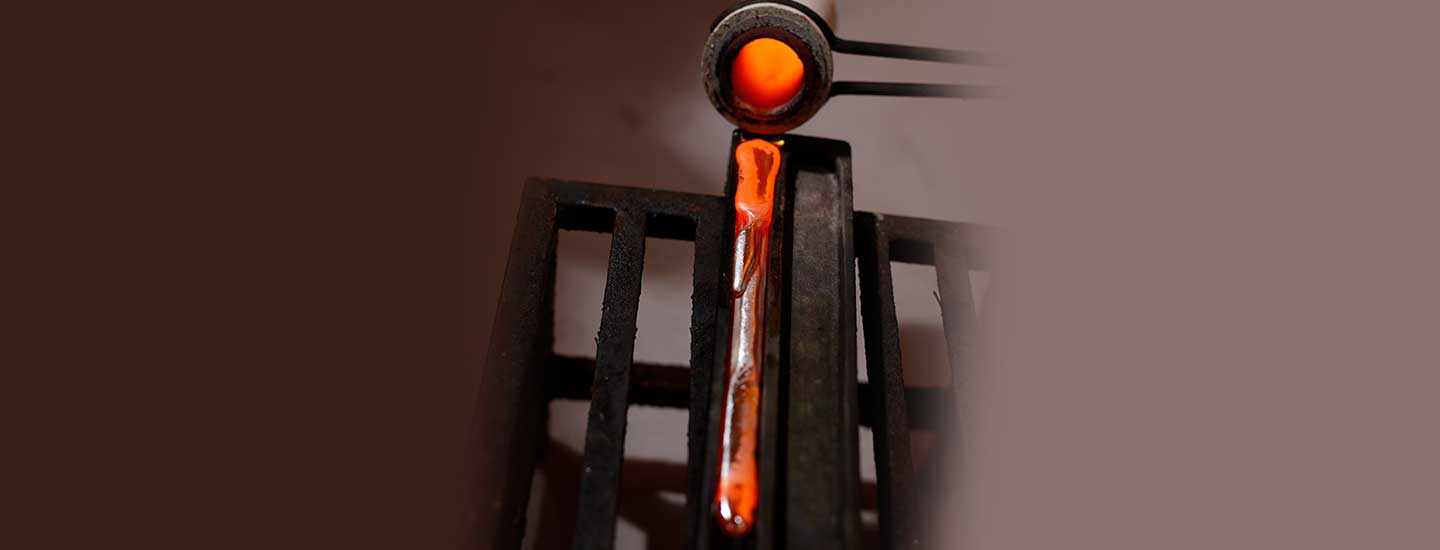
Jewelry Casting Process
Jewelry casting is a process in which a wax pattern is made into a jewelry mold and filled with melted precious metals like gold, silver, or platinum. This process is also called lost wax casting as the wax is melted or lost during the process. Most of the jewelry models created through wax carving or printing are encased in a plaster-like medium known as the investment. The casting procedures for gold and platinum are different as both melt at different temperatures. As platinum melts at a very high temperature, it requires a separate process and equipment. The most common methods of gold castings are:
Wax Model
This stage involves casting preparation with the wax piece or model. Based on the 3D rendition of the design, a wax model is carved or printed to represent the pattern of the finished jewelry. These wax models are attached to a sprue to form a tree. This forms a channel to allow the gold to flow through the tree.
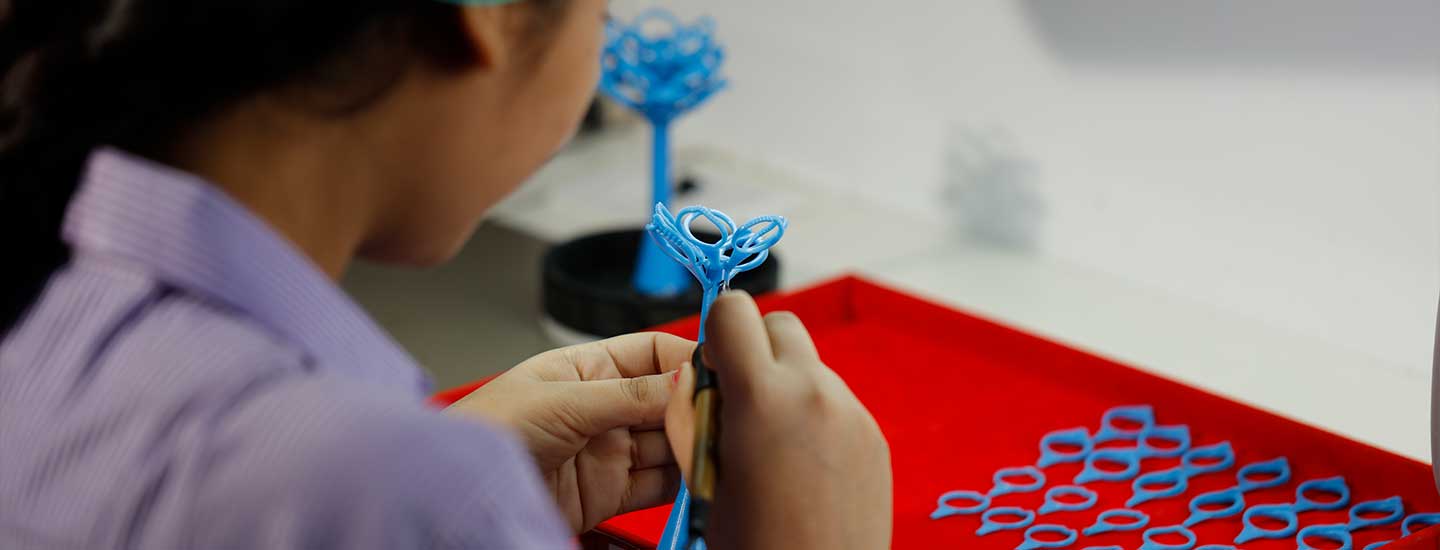
Investment
The tree with the attached wax or resin pieces is placed inside a metal flask and filled with investment material in form of a slurry. Once this slurry mixture settles, it hardens into a mold for the jewelry.
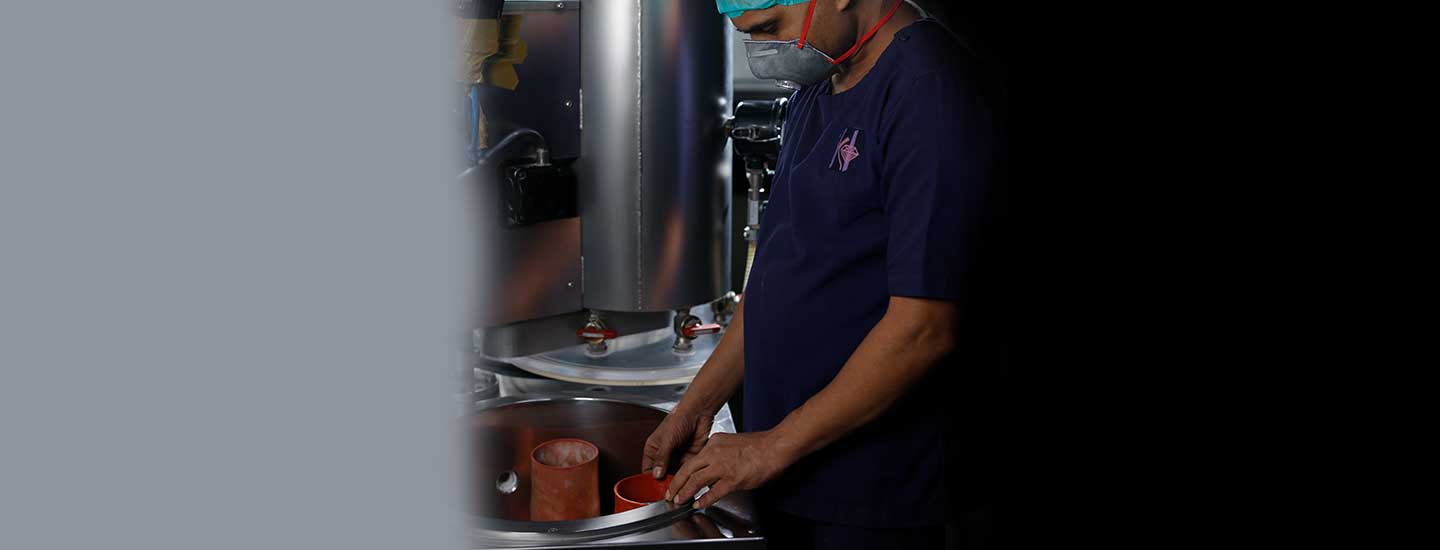
Burnout
The hardened investment mold or flask is placed in a special kiln at a high temperature for 12-15 hours. This causes the wax or resin to burn away and leaves behind a cavity in the place where the wax was. This becomes the final mold of the jewelry.
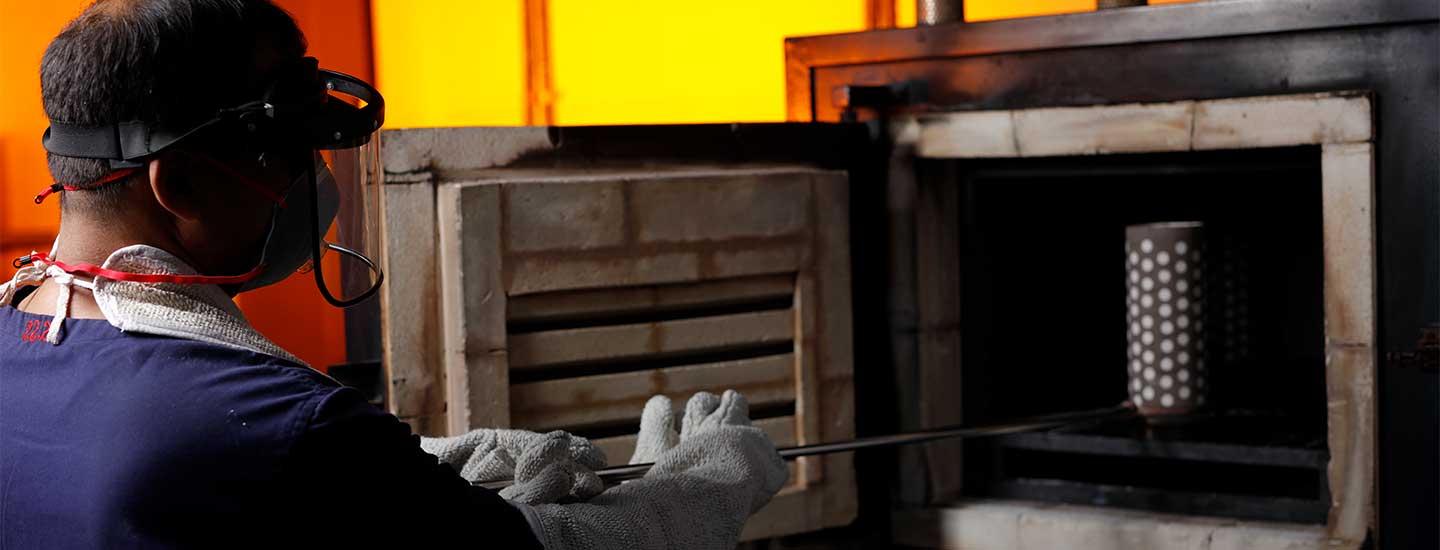
Melting and Casting
This process involves pouring molten gold into the hollow cavity of the wax-free mold. The melted gold can be poured directly into the mold, but now we have many other techniques which can give better results and quality of casting such as centrifugal casting, vacuum-assisted casting, and pressure casting. These ensure that the gold flows evenly into every area of the mold.
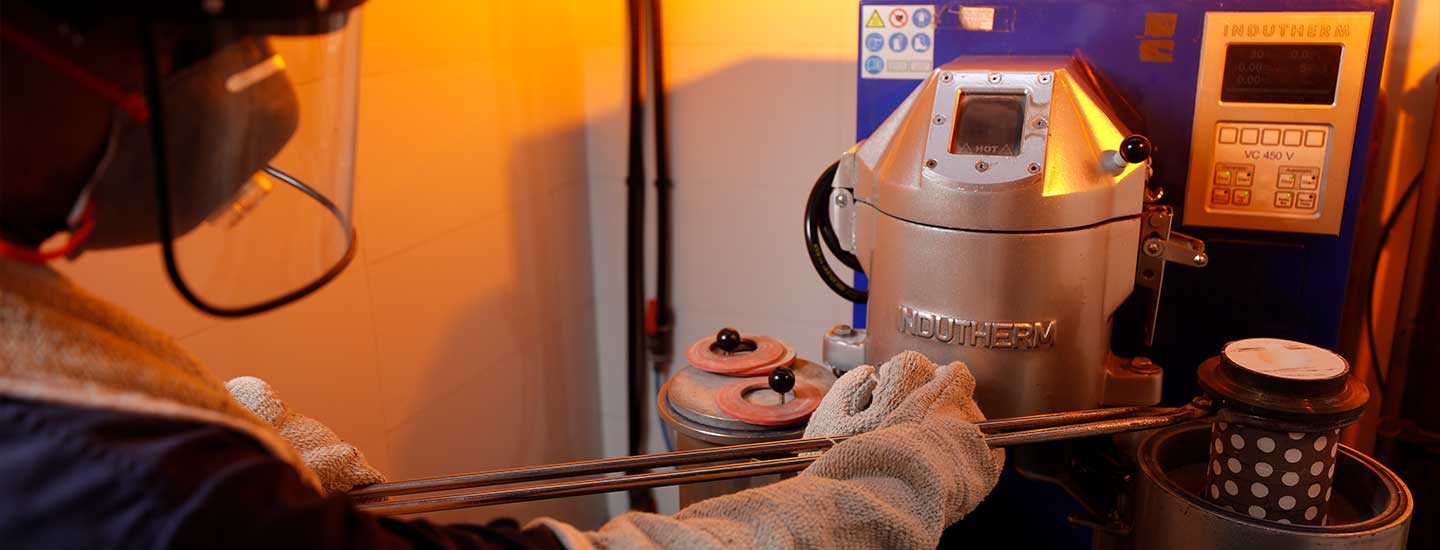
Divesting
This is the last stage of the casting process. Once the metal cools from the casting process, it needs to be removed from the investment material. This can be done through physical means such as placing the molds in a bucket of cold water which results in the investment material chipping away or through chemical means.
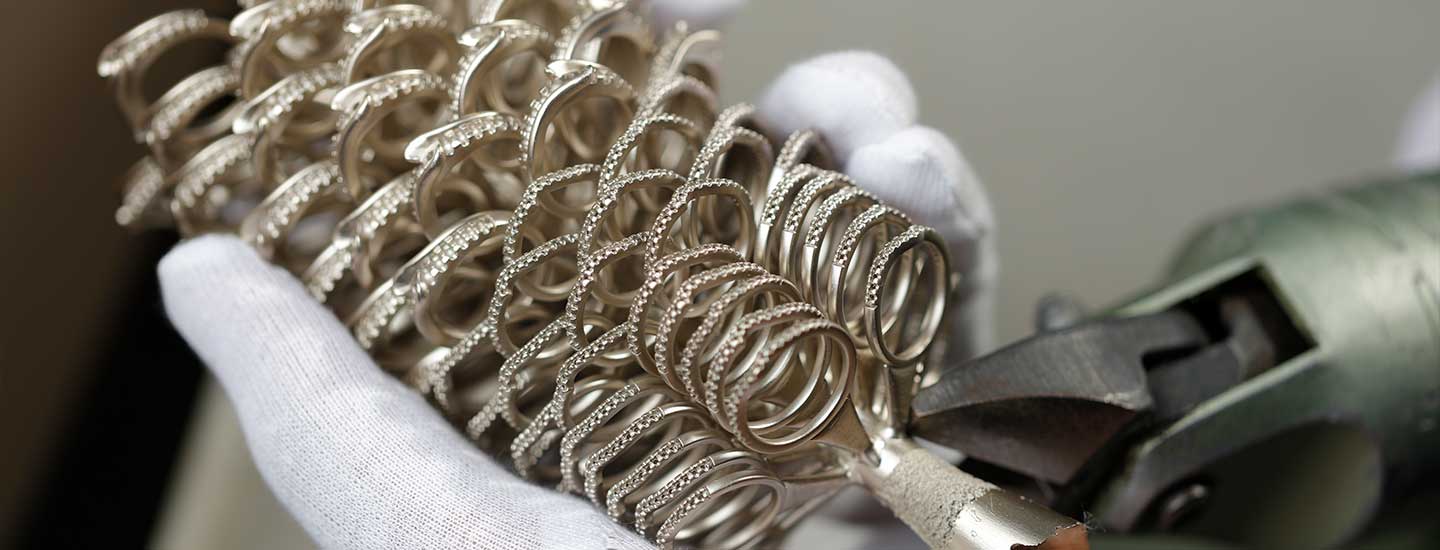
Casting with Different Metals
Gold Casting
Gold has been a classic choice for jewelry for ages, and for a good reason. It is
resistant to tarnishing and is very soft and malleable, which is why it has the
lowest melting temperatures among precious metals. For casting, the exact
temperature required for gold depends on the gold karat required for the jewelry.
Most jewelry has a mixture of alloy with gold, and karat refers to how much is the
composition of pure gold in a material.
Each gold variety is marked by how many parts out of 24 are made with gold e.g. 18
karat gold will have 18 parts of pure gold and others will be alloys. As pure gold
is very soft, it is very difficult to mold jewelry from it. For plain gold jewelry,
we can go up to 22 karat but if needed to be studded with diamonds or gemstones then
18karat and lower is preferred. Alloys are also required to change the color of gold
to white or rose as gold is originally yellow in color.
Silver Casting
Silver is beautiful but can be challenging to work within its pure form. It has a higher melting point than gold – about 1761 degrees Fahrenheit when pure – and its casting process may require fluxes or degassing. Sterling silver has become a front-runner in jewelry materials because the combination of silver and copper melts at a lower temperature and forms a stronger, more durable final product.
Platinum Casting
Platinum is a unique precious metal when it comes to jewelry casting. It is an
undeniably gorgeous material for finished pieces but is one of the most challenging
metals to work with. Platinum only melts at extremely high temperatures, and it
solidifies rapidly as it cools. While gold typically solidifies in around 20
seconds, platinum pieces can harden in 3-4 seconds which can make shrinkage and
porosity an acute concern.
The flasks and investments used for creating silver or gold castings aren’t suitable
for the extreme conditions needed to melt platinum. You need specific materials that
are resistant to refraction, thermal shock, and metal penetration. Platinum
castings, while stunning, require a unique level of attention, experience, and
preparation to create properly.